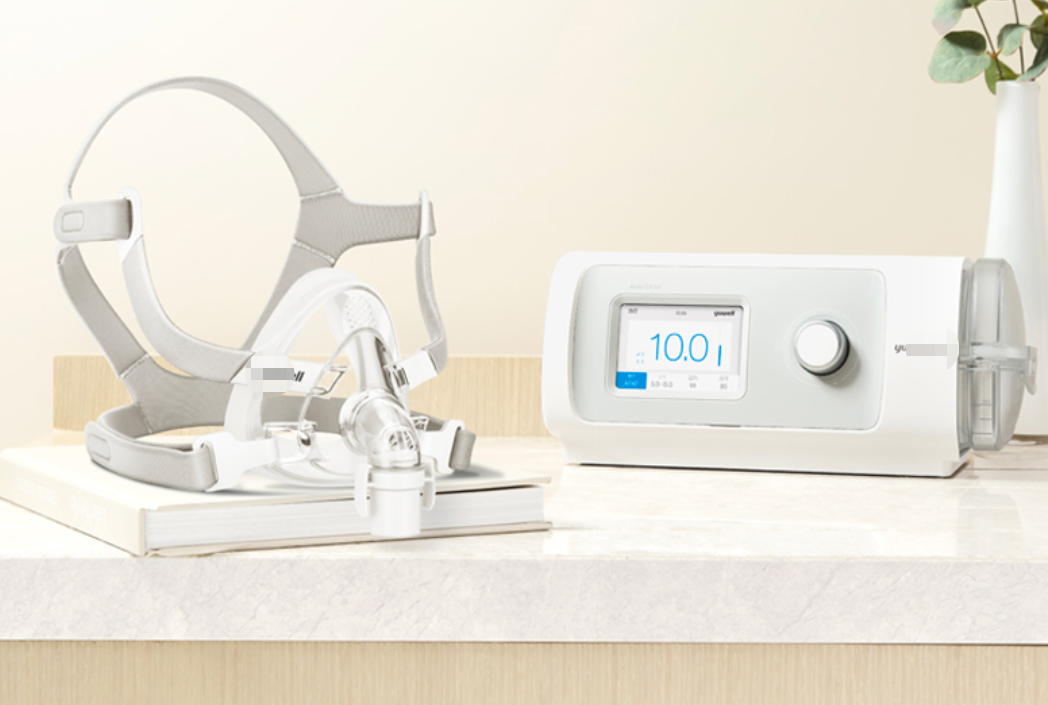
Solving Medical Mask Production Challenges with Innovative Materials
Challenges in Medical Mask Production In medical-grade product production, especially for breathing masks, functionality, safety, and durability are critical. Henry Precision faced several challenges in designing medical masks using Covestro PC-2458 (a high-temperature-resistant polycarbonate) and JAPEN Shin Etsu2090-40 (liquid silicone rubber, LSR). These materials meet FDA’s biocompatibility requirements and provide the necessary support, sealing properties, and performance. Material Compatibility and Bonding Issues Bonding liquid silicone to plastic components is essential for maintaining structural integrity. The high fluidity of liquid silicone can cause gas traps, degumming, and non-stick defects. To address this, the adhesive process had to ensure a strong, reliable