This case outlines the full coating process flow for a precision component, which includes solvent handling, filtration, surface treatment, coating, heat leveling, and UV curing. The target is to achieve a uniform, defect-free dry film with a thickness > 8.0 μm.
1. Material Storage and Handling
- Storage Temperature: 20–25°C (No refrigeration required)
- Filtration Requirements:
- First stage: 25 μm filter bag
- Second stage: 5–10 μm filter element
- Final stage: 1 μm absolute gel-type filter element
This ensures the coating material is free from particulate contamination before use.
2. Pre-Treatment Before Coating
- Environment: Cleanroom class 10,000 or above
- Optional Solvent Cleaning: If needed, to remove surface oil or dust
- Plasma Wind Treatment: Enhances surface energy and adhesion
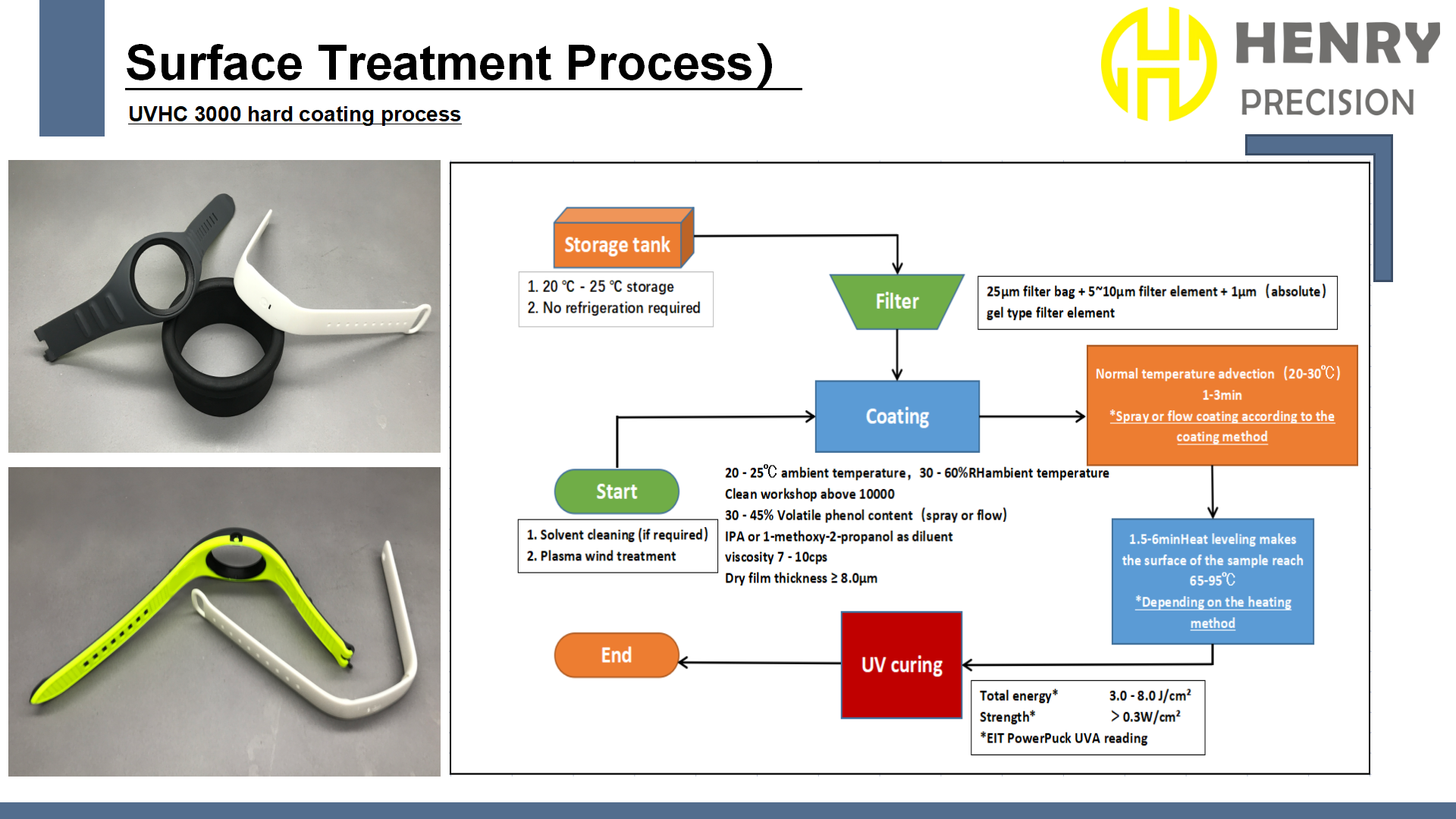
3. Coating Application
- Method: Spray coating or flow coating
- Conditions:
- Ambient temperature: 20–25°C
- Relative humidity (RH): 30–60%
- Volatile phenol content: 30–45% (depending on method)
- Diluents: PA (propylene glycol monoalkyl ether acetate) or 1-methoxy-2-propanol
- Target viscosity: 7–10 cps (ideal for even coating application)
4. Heat Leveling Process
- Purpose: To create a smooth and uniform surface before UV curing
- Duration: 1.5–6 minutes
- Temperature: Sample surface reaches 65–95°C (depends on heating method)
- Film Uniformity: Ensures coating flow and elimination of micro-defects prior to curing
5. UV Curing Process
- Dry Film Thickness: > 8.0 μm
- UV Energy Requirements:
- Total Energy: 3.0–8.0 J/cm²
- Intensity: > 0.3 W/cm²
- Monitoring Method: EIT Power Puck – UVA range reading
This step ensures complete polymerization of the coating, resulting in a strong, durable, and defect-free film.
Final Result
After optimization of filtration, plasma surface preparation, and heat leveling, the coating achieved:
- Excellent surface flatness
- Strong adhesion to substrate
- No visible particles, pinholes, or peeling
- Uniform thickness > 8.0 μm
- Stable UV curing performance across production batches
- If you’re looking for a full-process precision coating solution — including cleanroom operations, viscosity control, and UV curing — our Henry Precision engineering team can assist with process setup and technical validation tailored to your application.