Project Background
A premium European bathroom brand required a high-performance overmolded silicone nozzle for its latest showerhead. The nozzle needed to be thermally stable, anti-clogging, waterproof, and visually appealing—with extremely tight dimensional tolerances and medical-grade cleanliness standards.
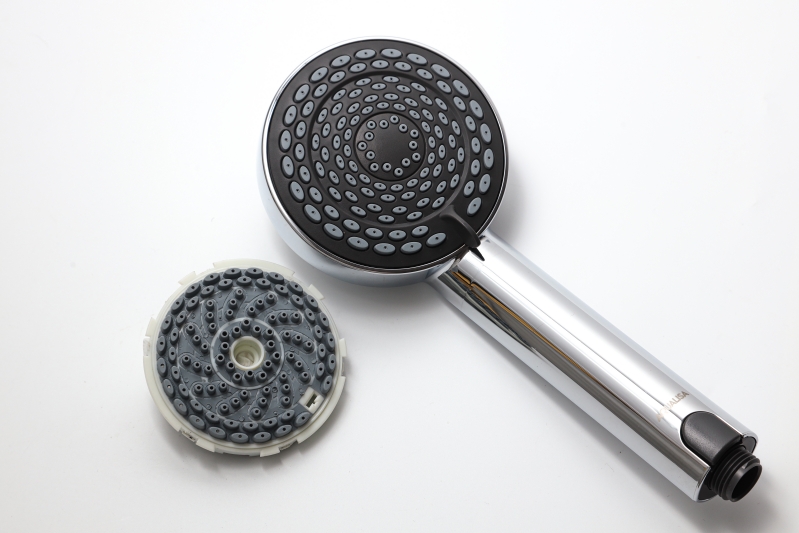
🧩 Component Structure
- Rigid Plastic Base: Covestro PC-2458
- Overmolding Material: WACKER LSR 3671-30
- Feature: Multiple fine silicone nozzles (0.5–0.7mm diameter, 0.3mm spacing), directly overmolded on a PC substrate.
🔧 Technical Challenges
- Temperature Sensitivity
PC material can deform above 120°C, which complicates LSR processing that typically requires high temperatures. - Bonding Area Defects
Gas traps and poor silicone adhesion at the PC-LSR interface can cause nozzle detachment and air leaks. - High-Density Micro-Brush Molding
Dense and fine nozzles are prone to short shots, incomplete filling, or breakage. - Stringent Appearance Standards
No black spots, flash, or odor is allowed—demanding high mold cleanliness and material purity.
✅ Henry Precision’s Solutions
- Precision Mold Design
Mold flow analysis and CNC machining ensured ±0.01mm tolerance accuracy. - Optimized Temperature Control
Multi-zone thermal management kept the PC substrate below deformation threshold. - Anti-Gas-Trap Design
Undercuts and vent structures were added at the bonding area to ensure complete filling. - Process Window Validation
Refined injection settings ensured no short shots or broken nozzles. - Class 100K Cleanroom Production
Dust-free manufacturing, multi-level filtration and degassing eliminated black spots, odor, and contamination.
🏆 Project Result
- Yield rate maintained above 98% in mass production
- Met strict European cosmetic standards
- Henry Precision appointed as long-term LSR overmolding partner
✉️ Need High-Precision LSR Overmolding for Shower Nozzles?
Contact Henry Precision for custom PC + LSR overmolding solutions—from tooling to cleanroom production.