Custom Injection Molding & Mold Manufacturing Services
We offer one-stop custom injection molding services, from sample to mass production. Our comprehensive solutions include custom mold design, material selection consulting, and precision injection molding manufacturing with strict quality control. Supported by an innovative R&D and engineering team, we have delivered high-quality, efficient custom injection molds and molded parts to global clients.
- Design support
- Rapid tooling services
- Various injection molding solutions
- Reliable delivery and stable performance
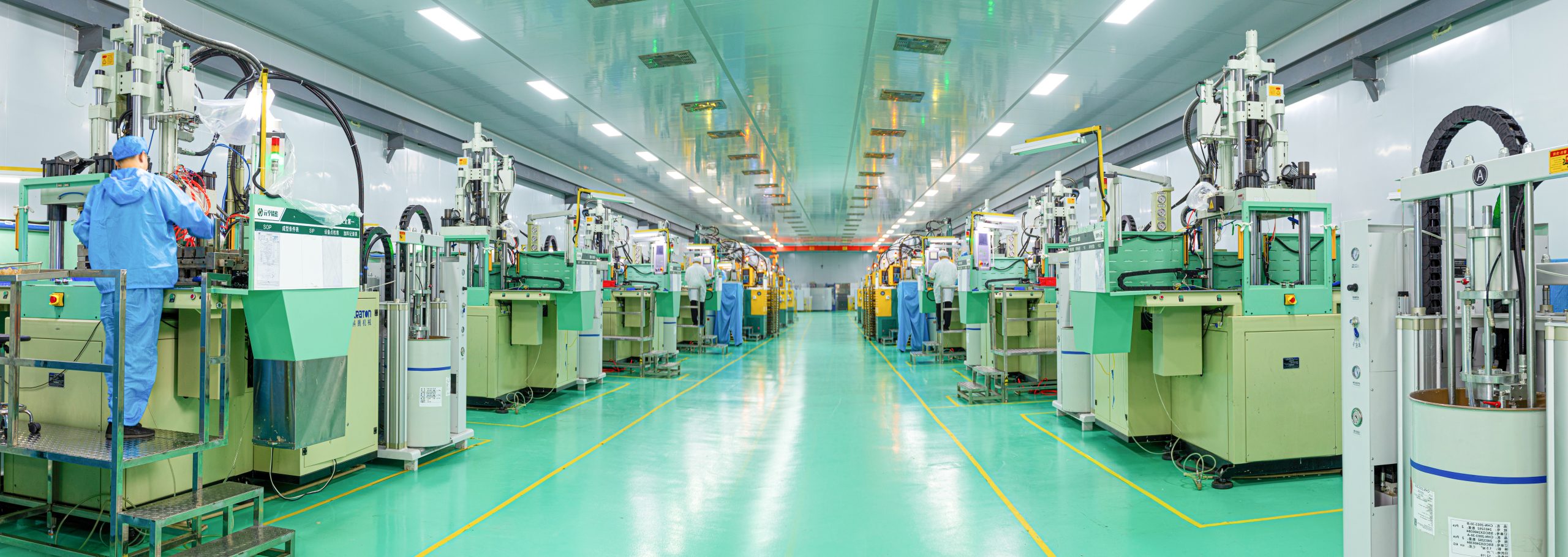
Our Capabilities | Our Mold Manufacturing Capabilities
Henry Precision employs advanced CNC machining, mold flow analysis, and automation technologies to ensure high precision and long mold life.
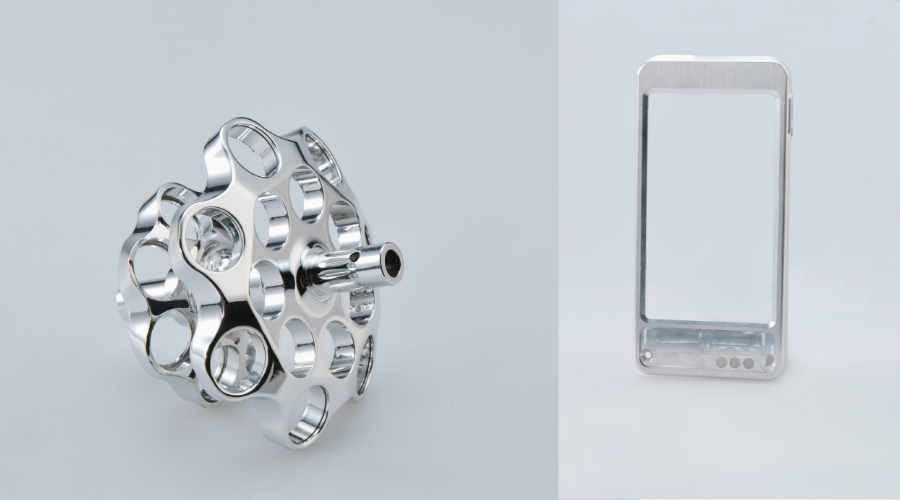
✅ High-precision steel molds, using imported Swedish S136, H13, and other high-wear-resistant steels, with mold life exceeding 1,000,000+ cycles
✅ Dimensional tolerance control up to ±0.005mm, ensuring molding accuracy
✅ Moldflow simulation to optimize cooling system and gate design, reducing deformation and shrinkage
✅ Runner balancing calculation to ensure product consistency in multi-cavity molds
✅ 5-axis CNC machining & EDM precision machining to ensure high precision of molds
✅ Automated assembly of mold standard components to improve production efficiency and reduce errors
✅ Supports single-cavity, multi-cavity, two-color, and overmolding molds to meet the needs of different industries
✅ Provides rapid mold trial & production optimization to ensure products pass verification on the first attempt
Types of Molds We Offer
Henry Precision specializes in high-precision molds, covering plastic, liquid silicone rubber (LSR), and complex molding processes.
✅ Suitable for medical devices, 3C electronics, automotive components
✅ High-precision mold tolerance of ±0.005mm, ensuring product consistency
✅ Suitable for medical-grade silicone parts, baby products, seals
✅ Vacuum-sealed, dust-free environment for production, ensuring contamination-free products
✅ Suitable for soft-hard combined products (e.g., electronic enclosures, waterproof components)
✅ Integrated molding process reduces subsequent assembly and improves sealing
✅ Suitable for large-volume production (e.g., consumer goods, packaging products)
✅ Optimized runner design ensures uniform dimensions for multi-cavity products
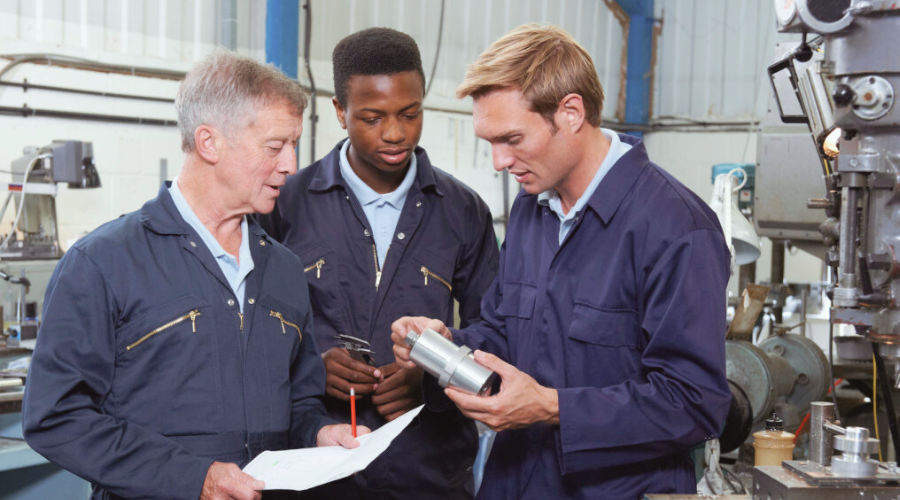
Rapid tooling service
After receiving drawings or samples from customers, we conduct detailed evaluations and validations, offering rapid sample mold development services. The following outlines the key steps in the process.
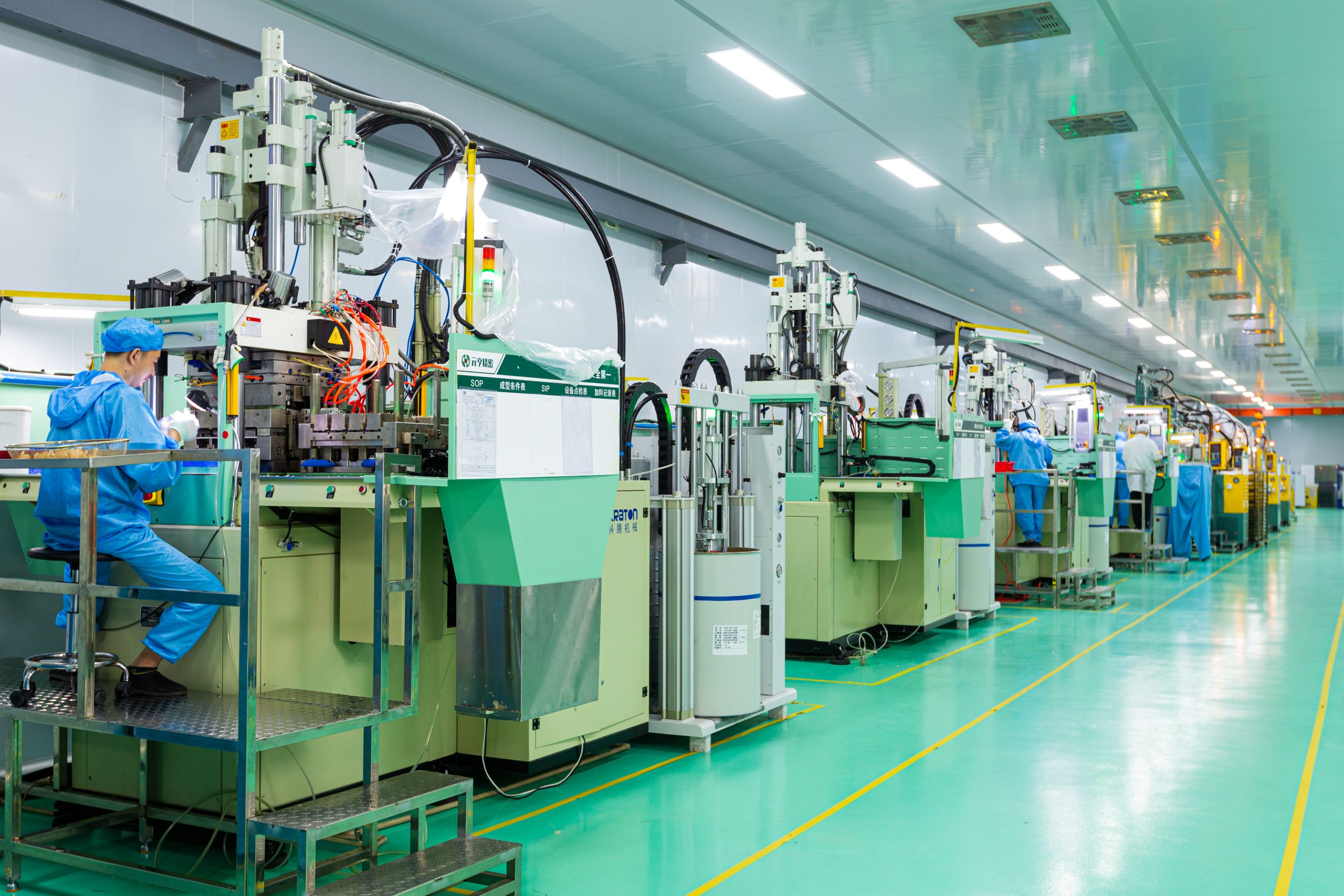
– After receiving customer drawings or samples, our technical team performs a thorough assessment of the product’s structure. This includes identifying potential design issues, such as thin walls, thick ribs, or buckling, and evaluating their impact on functionality and the molding process.
– The assessment also involves precise dimension measurements and 3D modeling comparisons to ensure accurate design implementation and prevent structural issues during production.
– Appearance design is critical, and our technical team collaborates closely with customers to ensure the product is both structurally sound and visually appealing, aligning with market trends and consumer preferences.
– When necessary, we provide professional design recommendations, including color selection and surface texture treatments, to enhance the product’s market competitiveness.
– After finalizing the structure and appearance, we utilize advanced rapid tooling technologies, including CNC machining and 3D printing, to shorten mold-making cycles and quickly meet customer needs.
– Despite the fast turnaround, our rapid mold-making process adheres to strict accuracy standards, ensuring custom injection molds precisely reflect the product’s design intent.
– After the mold is completed, engineers determine the optimal injection process parameters, such as injection pressure, temperature, and cooling time, to ensure product quality and enhance production efficiency.
– During this stage, multiple trials are conducted using physical samples to test and validate the effectiveness of the process settings, ensuring all products meet established quality standards.
– The mold trial evaluates both the quality of the mold and the product’s appearance and dimensions to ensure they meet specifications.
– Based on trial results, adjustments may be made to the process parameters or the mold itself to achieve the best production outcomes. This step is crucial for ensuring the final product’s quality and consistency.
Factory Tour
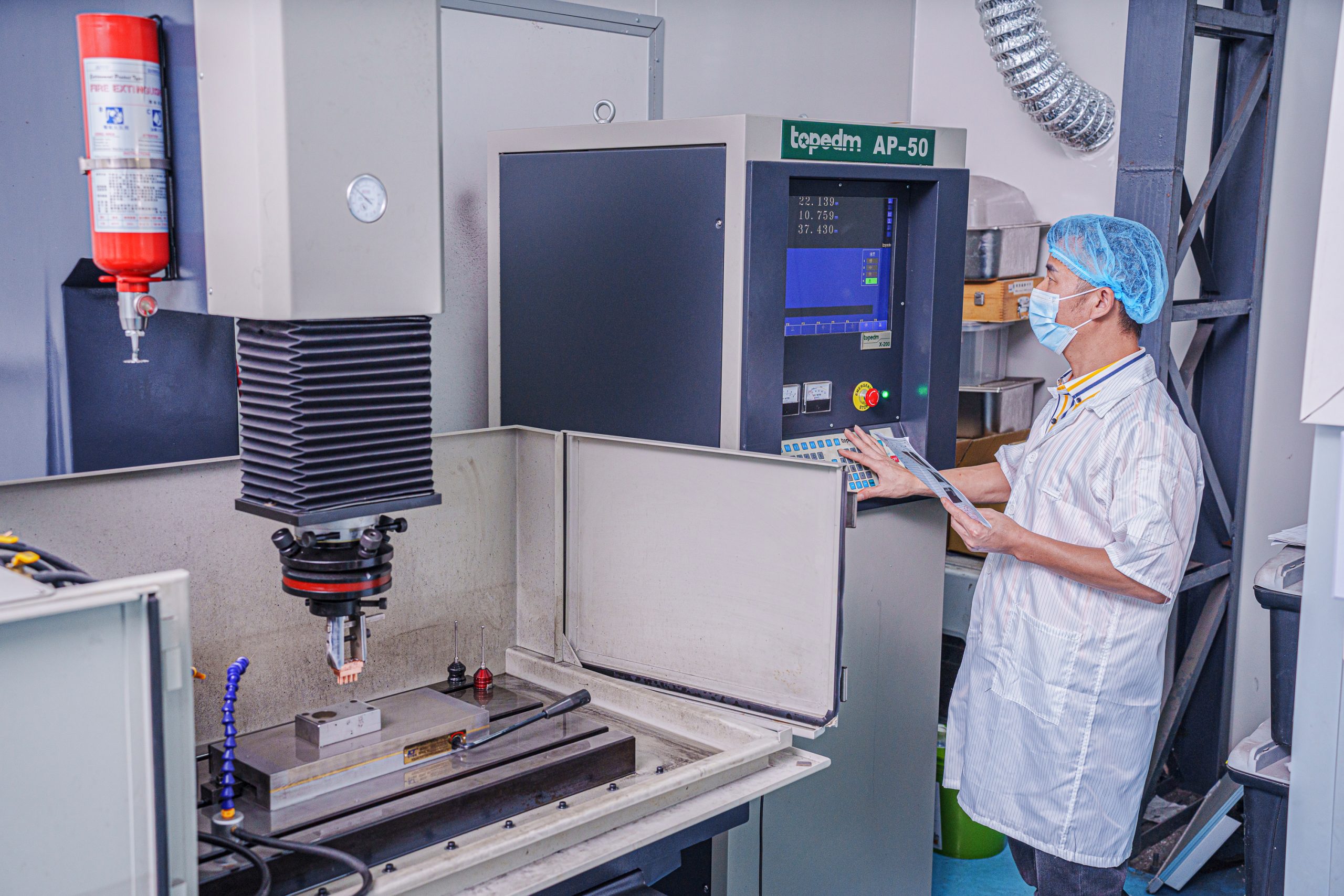
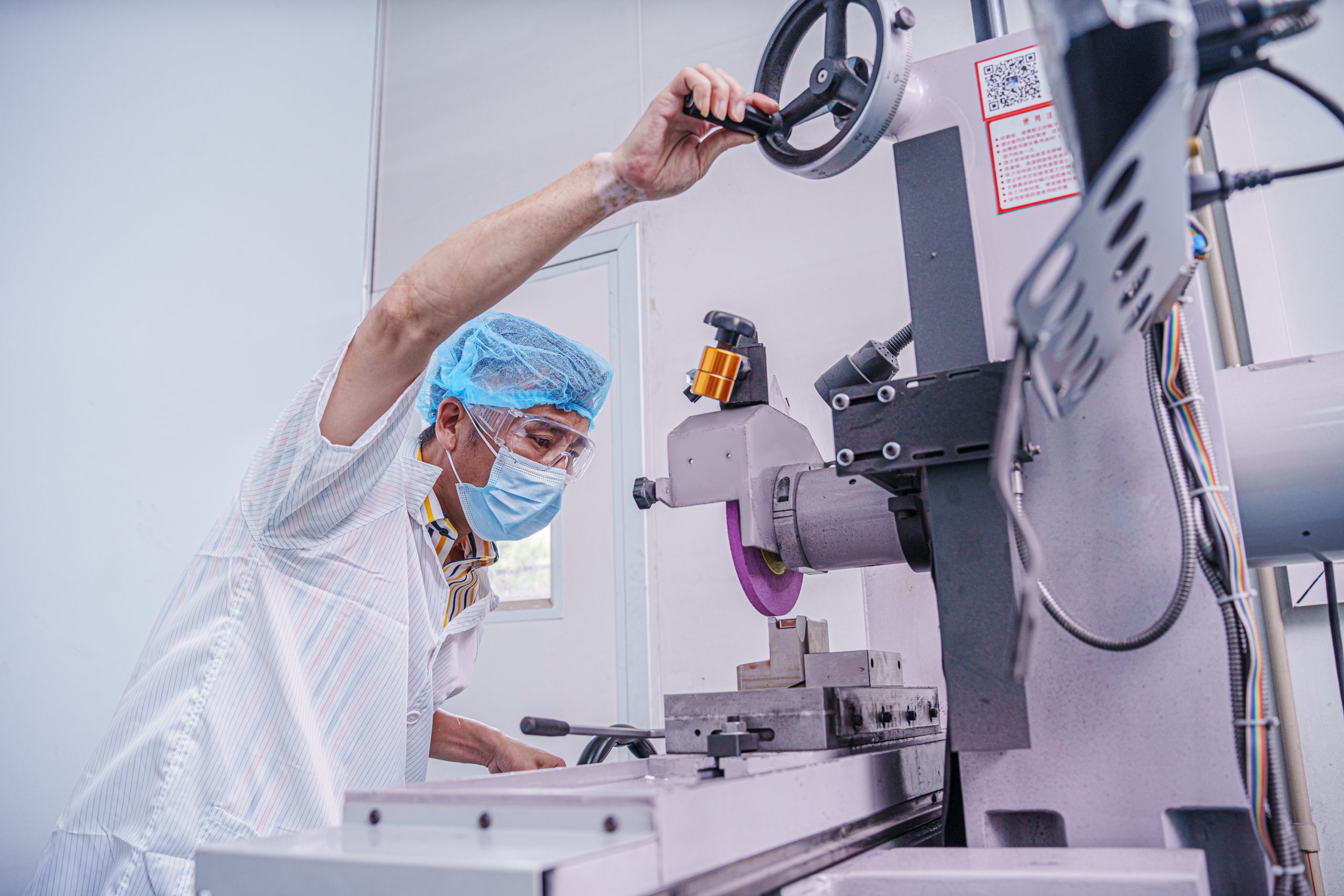
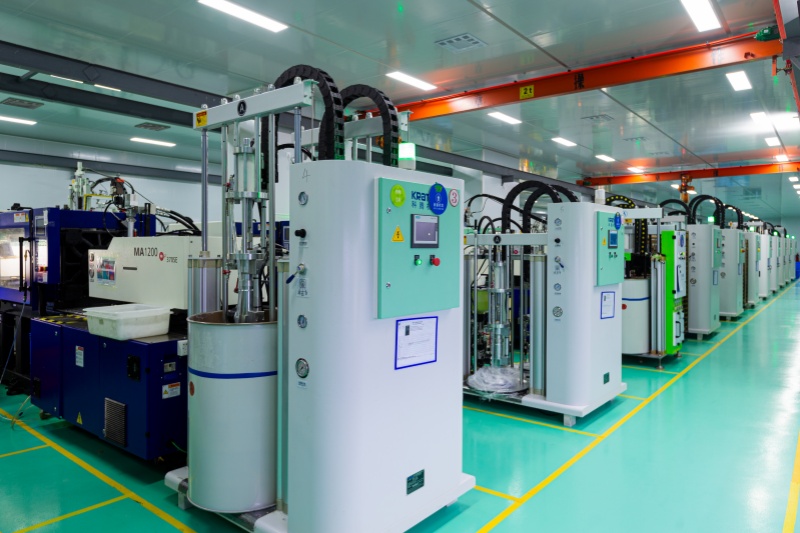
Material Used in Custom Injection Molding
Materials for Mold Manufacturing
Mold materials commonly used for injection molds include the following
1. steel | – P20 steel: has good machining performance and polishing performance, commonly used in general requirements of the injection mold, such as the production of large quantities, low requirements of plastic products. | – 718 steel: better performance in terms of strength and toughness, suitable for the production of medium volume, a certain degree of precision requirements of the injection mold. | – S136 steel: excellent corrosion resistance and polishing performance, commonly used in the production of high surface quality requirements, the need for rust-resistant injection molds, such as the production of transparent plastic parts or corrosive plastic molds. | – NAK80 steel: with excellent mirror processing performance and electrical discharge machining performance, suitable for high-precision, high mirror surface requirements of the injection mold. |
2. aluminum alloy | – 6061 aluminum alloy: has good processing performance and thermal conductivity, but relatively low strength. Commonly used in small, simple structure of the injection mold, or mold weight requirements of the occasion. | |||
3. Copper alloy | – Beryllium copper alloy: with high thermal conductivity and wear resistance, often used in injection molds that require rapid heat transfer or frequent friction parts, such as sprue sets, cores and so on. | |||
4. Hard Alloys | – Tungsten steel: extremely high hardness, good wear resistance, suitable for the production of life requirements of very high, harsh molding conditions of the injection mold parts, such as mold cores, inserts and so on. |
Materials for Injection Molding
Food-Grade Silicone, Medical-Grade Silicone, Low-Temperature Silicone, etc. | ||||
PP, PC, PS, ABS, PA, POM, PMMA, PE, PVC, PBT, etc. |
Our Mold Manufacturing Process
Henry Precision adopts a systematic mold manufacturing process to ensure accuracy and reliability in every step.
1. Requirement Analysis & DFM Evaluation
✅ Communicate with clients about product requirements and material selection, ensuring the mold design meets production needs
✅ Perform DFM (Design for Manufacturing) evaluation to optimize product structure and reduce production defects
2. 3D Design & Moldflow Simulation
✅ Use software such as Siemens NX, SolidWorks, and Moldflow for precise modeling
✅ Optimize cooling systems and gate placement to reduce molding defects like warping and shrinkage
3. High-Precision Mold Manufacturing
✅ CNC precision machining ensures critical part tolerances within ±0.005mm
✅ EDM spark erosion machining is used for high-precision molding of complex structures
4. Mold Trial & Quality Testing
✅ Conduct T0-T2 mold trials to verify molding performance
✅ Use CMM (Coordinate Measuring Machine) and optical inspection to ensure products meet design specifications
5. Delivery & Maintenance Support
✅ Provide mold operation training to ensure efficient production
✅ Offer mold maintenance and optimization services to extend mold lifespan
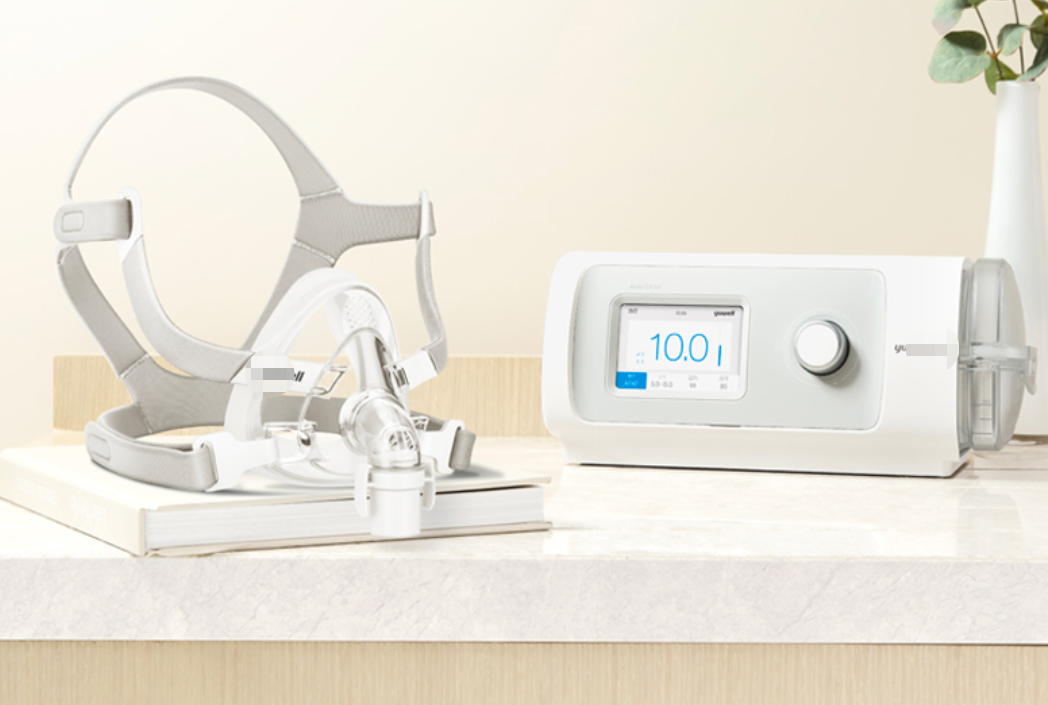
Solving Medical Mask Production Challenges with Innovative Materials
Challenges in Medical Mask Production In medical-grade product production, especially for breathing masks, functionality, safety, and durability are critical. Henry Precision faced several challenges in designing medical masks using Covestro PC-2458 (a high-temperature-resistant polycarbonate) and JAPEN Shin Etsu2090-40 (liquid silicone rubber, LSR). These materials meet FDA’s biocompatibility requirements and provide the necessary support, sealing properties, and performance. Material Compatibility and Bonding Issues Bonding liquid silicone to plastic components is essential for maintaining structural integrity. The high fluidity of liquid silicone can cause gas traps, degumming, and non-stick defects. To address this, the adhesive process had to ensure a strong, reliable
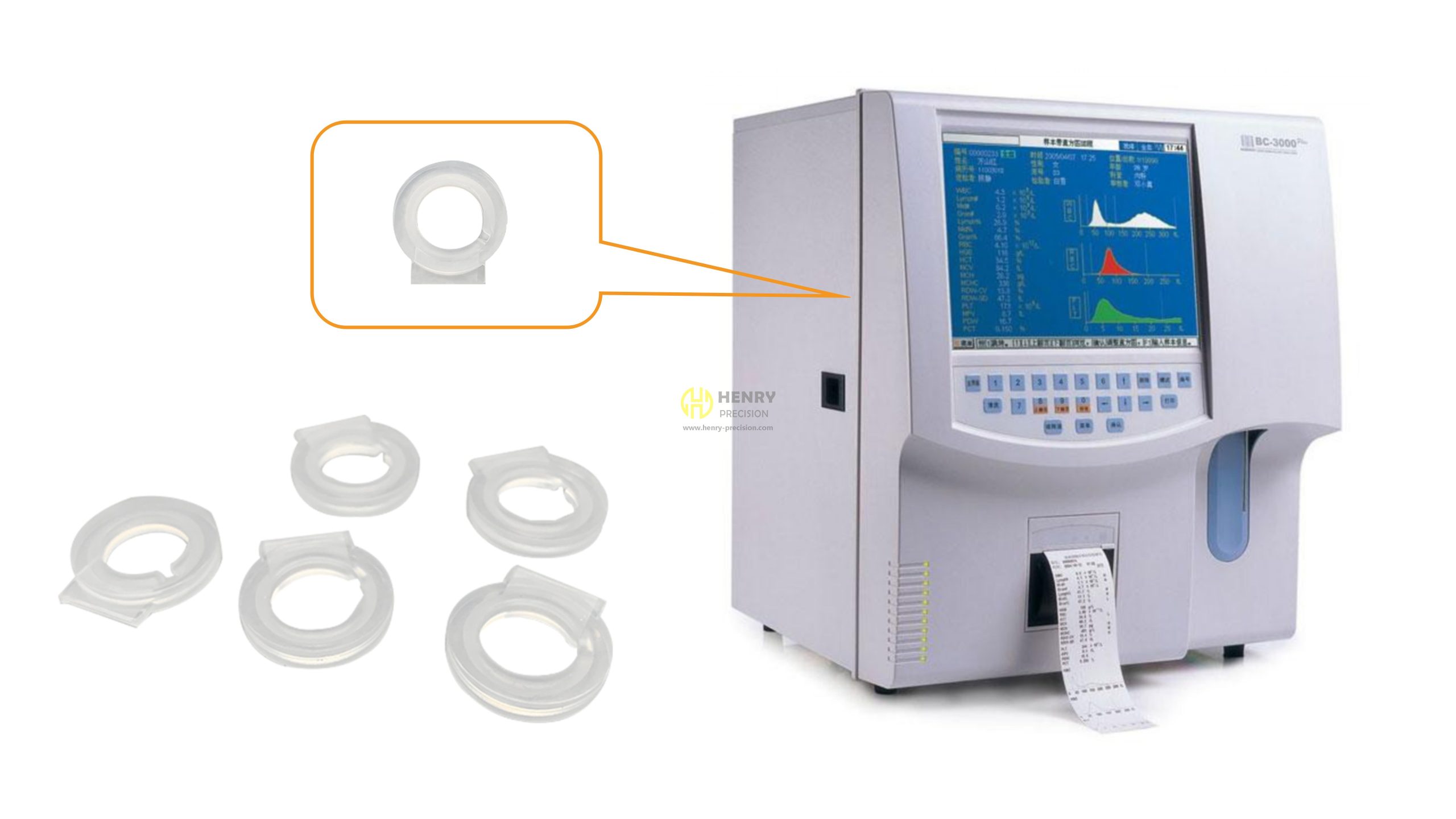
High-Performance Sealing Rings for Medical Devices
In the production of sealing rings for medical devices, maintaining precision and ensuring high-quality performance is crucial. Henry Precision recently encountered several challenges while manufacturing a sealing ring with WACKER 3038-70 silicone material. The product’s small size, internal instability, and complex structure required advanced design, meticulous attention to detail, and high-precision mold processing. Challenges Internal Size InstabilityThe sealing ring had a relatively small internal size, which was prone to instability. This caused issues such as partial silicon filling, leading to potential quality defects. The solution required careful mold design and machining precision to ensure stable production. Multiple Cavities and
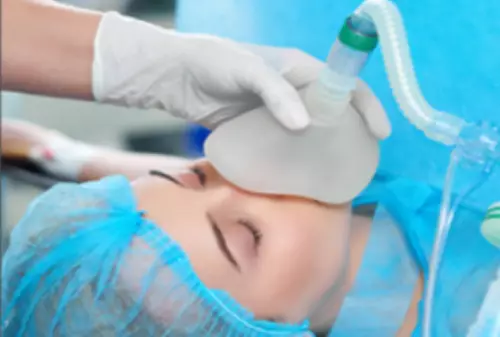
Efficient Prototype Molding for Quality Respiratory Masks
For this project, Henry Precision was tasked with producing a respiratory mask using a rapid prototype mold. The product was made from Liquid Silicone Rubber (LSR) and required precise manufacturing to meet high standards. The mold size was Wx300 Lx300 H (mm), and it featured a cavity of 1. The delivery time was set at 10 days to meet the customer’s needs. Manufacturing process Rapid prototype mold (referred to as sample mold) Material LSR Insert Material Steel S136 Product size 124x109x73mm Mold size Wx300 Lx300 H (mm) (Lung Kee standard mold holder: 3030) Cavity 1 Delivery time 10 days Project
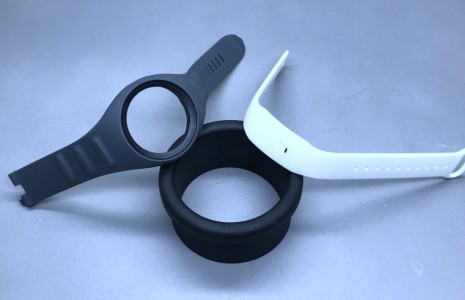
This is an editable piece of text,This is an editable piece of text,This is an editable piece of text,
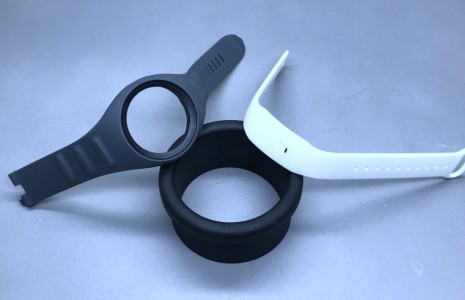
This is an editable piece of text,This is an editable piece of text,This is an editable piece of text,
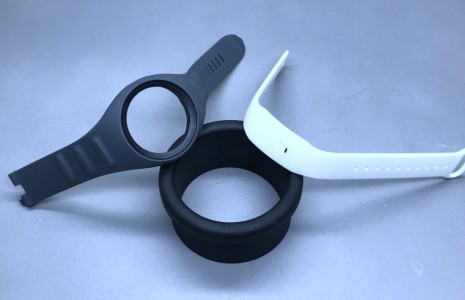
This is an editable piece of text,This is an editable piece of text,This is an editable piece of text,
Let’s build the future with innovation.
Please provide the following details to help us better understand your needs and get in touch with you as soon as possible.
You can send us 3D drawings in STL, STEP, IGES and 2D drawings in PDF. We will provide accurate quotations within 24 hours.
From concept to completion, we provide a one-stop silicone mold manufacturing service.